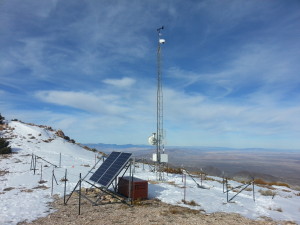
Electronics and field research are more intertwined than ever. With the advent of inexpensive multifunction dataloggers, more and more research projects are deploying sensor systems with the intent of obtaining multiple years of data. Long term observation sites have been using standalone electronic systems for decades, and are increasing in scale. As newer technology is implemented in environmental monitoring, for instance cameras or high-speed data connectivity, the potential power requirements increase accordingly.
For the majority of deployment types, the common failure point is arguably the power supply system. Data gaps, malfunctions, and other problems result from power system failure. Very often, researchers will either 1) not be aware of the problem until much later (unless they have implemented some sort of telemetry) or 2) scramble to the field to find and fix the problem. One could make the argument that this is a pretty inefficient way to do research, and lowers the overall quality and impact of the studies being conducted. It is certainly not how I prefer to spend my time.
So, what are some of the straightforward changes that can be made to field sensor systems that increase reliability?
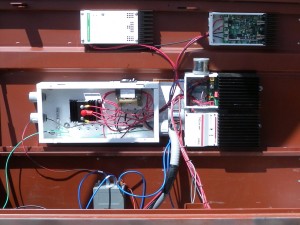
- Battery backup – even if your system is tied to “line power”, it is crucial that you configure the power supply such that there is a battery backup of some decent capacity available to power the system in case of line power loss. The best case is to power your system from a battery bank, and have the batteries constantly charged from the line power source. If you don’t have two distinct power sources, run a parallel-redundant system anyway. If all batteries are connected in a single bank, one cell failure in winter can potentially kill the whole system. Passively combining DC power from two isolated battery/charging systems can be done without introducing fancy control circuitry. While the extra expense of purchasing batteries and associated electronics may seem excessive, loss of data or extra trips becomes even more expensive, and quickly.
- Battery capacity – many or most field sensory systems are exclusively battery-powered, with charging sources being solar, wind, or even fuel-powered generators. Issues with generation choices aside, the weak point in this system is usually the battery itself. Often in an effort to save money, the researcher will not purchase enough battery capacity to run their system comfortably for long intervals between charging. This lack of capacity usually causes additional problems as battery voltage drops, such as incurring datalogger malfunctions, reducing battery longevity, or even killing the battery altogether (see below). These potential research-killers can be minimized by scaling the battery bank so that the storage capacity will only fall below 50% under very rare and unusual circumstances.
- Low-Voltage Disconnect – very often, the reason a battery system fails is because of excessive drawdown. Most battery types are not designed to be discharged below a certain level for extended periods of time. This is related to capacity (above), but also the lack of shut-off protection in the event of prolonged absence of charging energy. Installation of automatic circuit shut-off protection should be considered as crucial as any other component in the power system. Commonly termed “Low Voltage Disconnects” (or LVDs), these devices are usually separate from solar and other charge controllers (although some are built-in). LVDs are installed between the battery and the load (the dataloggers, radios, and other devices). There are many different types of LVDs available (and more are showing up on the market all the time), but essentially you want to ensure that the LVD is rated for a decent margin above your expected maximum current and that you can adjust the cutoff voltage to match your power management plan.
- Wiring protection – another common source of field electronics angst is damaged wiring. Protecting wiring from UV exposure, wind/ice, and animal disturbance should always be part of a field installation. An inexpensive and surprisingly robust wiring protector is light-duty irrigation drip-line (1/2″ to 1″ diameter). This tubing is designed to survive exposure to the elements and is not as much of a target for animal disturbance as softer, more flexible tubing types. If particularly-persistent rodents or other mammals are known to be in your research area, consider using metal-lined wiring conduit.
Liberal use of circuit breakers, surge protection, and LVDs can save a lot of downtime by protecting vital equipment like batteries and network devices. - Circuit-breaker and surge protection – rather than wiring all devices directly to the battery or other power source, using circuit-breakers allows for short protection as well as a convenient cut-off for power cycling and servicing. In the case of DC-power field systems, it is not generally important to size the breaker close to the expected load. Instead, use a breaker with at least twice if not more the expected current capacity of the system. Surge protection for lightning-related transitory voltage is highly recommended to channel high voltages to ground. Some protectors can be installed on the general system close to the charge controller and batteries, while others are designed for individual conductor protection (which is useful for sensor wiring). If wiring is run between enclosures or being distributed across the landscape of a field site, use of breakers and surge protection becomes more important because the wires are more likely to be compromised or exposed to transient voltages from lightning.
Be proactive, not reactive. Design your system to survive common field problems so that an automated field site doesn’t become a time and money liability. These suggestions and more can be found at the Best Practices pages maintained by the Envirosensing cluster at the Federation for Earth Science Information Partners.

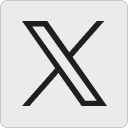
